Ahhoz, hogy megértsük a mai szemestermény-szárítás trendjeit és igényeit, egy kicsit nézzünk vissza a korábbi időszakokra, hogy milyen fejlődésen ment keresztül a terményszárítás az elmúlt néhány évtizedben.
A MÚLT
A rendszerváltás előtti időkben a terményszárító-feldolgozási kapacitást az adott gazdasági egység (pl. TSZ) nagyságához alakították ki. Ez azt jelenti, hogy egy szántóföldi termelési egységet nagyságrendileg átlagosan 800 hektár méretben határoztak meg, és ehhez a mérethez igazították a gépesítés és kiszolgáló technológiák kialakítását. Voltak régiónként eltérő egyedi gazdasági méretek is, de esetünkben a szárító-feldolgozási kapacitására vonatkozóan ezeknél is az említett 800 ha volt a bázis mérték. (Ikresítették a szárítókat két ugyanakkora mérettel, vagy több szárítótelep-bázissal hozták létre.) Ezekre a méretekre fejlesztették ki elsősorban a Bábolna típusú szárítókat, valamint a kevésbé elterjedt Sirokkó és Kolman típusokat, illetve a külföldről bevezetett szárítókat is ez a méret határozta meg, mint amilyen például az orosz DSZP vagy az amerikai Berico volt.
Az adott kor követelményeinek ezek a szárítógépek maximálisan megfeleltek, és kifejezetten korszerűek voltak. Ekkor természetesen nem az energiatakarékosság és a környezetvédelmi megfelelőség volt a fókuszban, hanem a minél nagyobb töltőtömeg és a nagy mennyiségű szárítás adott időegység (szárítási szezon) alatt. A berendezések mellé külön hőellátó egység volt építve hatalmas meleglevegő-befúvó ventilátorokkal. A pakura vagy később gáz és villamos energia fogyasztása nem volt kérdés, mivel nem ezeknek a jellemzőknek a csökkentése volt a fejlesztés fő iránya, mert ezek „korlátlanul” rendelkezésre álltak. A környezetvédelmi megfelelőség sem volt kérdés, hiszen ezeket a telepeket messze a lakott területtől alakították ki, illetve a kilépő levegő szabadon távozott a szárítógépből, mely természetesen vízgőzzel telített, valamint léhával, porral és káros anyaggal gazdag elegy volt. A betakarított termény minőségi megóvása sem volt az elsők között, mivel a terményt főleg a saját állattenyésztő telepek használták fel. Itt nemcsak a törtszem arányára gondolhatunk a szárítóból kijövő termény esetén, hanem a pakurás tüzelés károsanyag-hatására is, mely a gázra történő átállás után azért nagyban megváltozott.
MEGVÁLTOZOTT FEJLESZTÉSI IRÁNYOK, BŐVÜLŐ PIAC
A rendszerváltás és privatizációk után elsődlegesen a modernizálás került előtérbe, mivel erre az időszakra a szárítógép-állomány nagyon elöregedett. Ekkor írták ki célzottan az ilyen fejlesztésekre vonatkozó állami támogatásokat, valamint az európai uniós forrásokat is bevonó pályázatokat, melyek kifejezetten népszerűek és sikeresek voltak. Mivel a fent említett szárítókat nem modernizálták az évek során (kivételt a Bábolna szárítók jelentettek a 2000-esévek elejétől, melyeket úgynevezett „adapterezéssel” láttak el a meglévő szárítók korszerűsítésére, illetve megjelent az új B3-15 típus is), így jelentek meg folyamatosan a külföldi gyártók berendezései, melyek már egy más műszaki színvonalat képviseltek. Jelen áttekintésben, hogy jobban követhetők legyenek a fejlődés irányai, a Bábolna típushoz hasonló kaszkád rendszerű szárítókat vettem alapul, tudva azt is, hogy több más rendszerű szárító is van a hazai piacon, de általánosságban a fejlesztési irányok energetikára és környezetvédelemre vonatkozóan ugyanazok. A szárítógépbe beépített hőellátó egységgel, hővisszanyeréssel, szigetelt oldallemezekkel, zárt rendszerű optimalizált szívott légtechnikával a szárítólevegő kilépő oldalán (mely egyből kisebb töltőtömeget is indukált ugyanazon feldolgozási teljesítményhez), modern vezérléssel és környezetvédelmi feltételeket is jobban kielégítő megoldásokkal. Ezeket a jellemzőket az energetikai mutatók kiegészítésével korábban – amikor használatos volt még a pályázatokhoz a Gépkatalógus – még korszerűségi mutatóval is jellemezték (1. kép.).
A beruházások feldolgozókapacitásának a nagyságrendje elsődlegesen a Bábolna szárítók 15 tonna/óra teljesítményének környékére fókuszáltak (lenti leírásainkban is ezt a típust vesszük alapnak összehasonlításul mint a legelterjedtebb hazai típust a korábbi időkből), így a 10 és 20 tonna/óra teljesítményű szárítók voltak a legnépszerűbbek. Itt jegyezzük meg, hogy a vízelvonás és fűtési hőmérséklet tekintetében is változtak a teljesítményspecifikációk, de a köztudatban lévő nagyságrendeknek megfelel ez a teljesítmény-összehasonlítás.
ÁTALAKULT IGÉNYEK
A következő nagyobb változást a földbirtok-tulajdonszerkezet átalakulásának időszaka hozta, mely azt eredményezte, hogy a beruházók kifejezetten a saját területükre méretezve és a környékbeli bérszárítás lehetőségeit figyelembe véve fogalmazták meg a feldolgozási kapacitásra vonatkozó teljesítményigényeiket. Itt már az 5 tonna/óra teljesítménytől a 30 vagy akár 45 tonna/óra teljesítmények is igényként merültek fel. Előtérbe került az üzemeltetés gazdaságossági mutatóinak minél jobb értéke, mivel például az „új rendszerben” a megtérülést kifejezetten nézték a finanszírozhatóság oldaláról, illetve a bérszárítás lehetőségei is indukálták ennek a mutatónak a minél pontosabb meghatározását. Kiemelt szerepet kapott a környezetvédelmi megfelelőség, különösen a zaj- és porkibocsátás tekintetében, mivel egyrészt szigorodtak a hatósági előírások, melyeket mérésekkel is kell igazolni a használatba vételhez, valamint a megvalósítandó beruházás távolsága a lakott területhez gyakran egyre közelebb került.
ENERGIATAKARÉKOSSÁG, TELJESÍTMÉNYNÖVELÉS
Ezek után az előzmények után jutunk el oda, hogy egy ma korszerűnek nevezhető kaszkádrendszerű szárítógép méretét és töltőtömegét tekintve, ha összehasonlítjuk egy Bábolna típusú szárító méretével és töltőtömegével, akkor a 15 t/ó teljesítmény helyett 25 t/ó teljesítményű szárítót kapunk, köszönhetően a folyamatos fejlesztéseknek (2. kép).
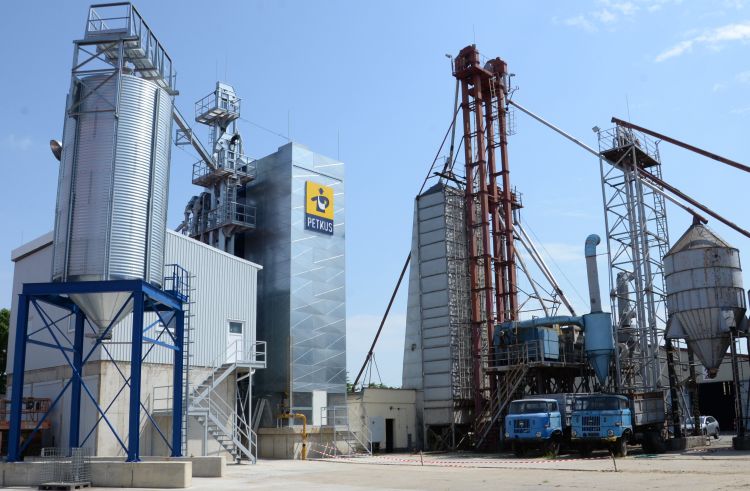
Hőellátását és légtechnikáját tekintve nagyságrendekkel kíméletesebb terményszárítást biztosít, ami egyben egyenletesebb és homogén vízelvonást is jelent a régi technológiákhoz képest, mely által a tört szemek aránya elhanyagolható a szárítóból kijövő anyagban, illetve a hősérült vagy égetett szemek aránya teljesen el is tűnt a minőségi vizsgálatok alapján. A hőellátást tekintve ma már modulált vezérléssel rendelkező gázüzemű „szőnyeg” vagy „sor” égőket alkalmaznak, melyek részét képezik a szárítótestnek, és teljesen egyenletes hőeloszlást biztosít a szárítógép teljes szélességében (3. kép, 1).
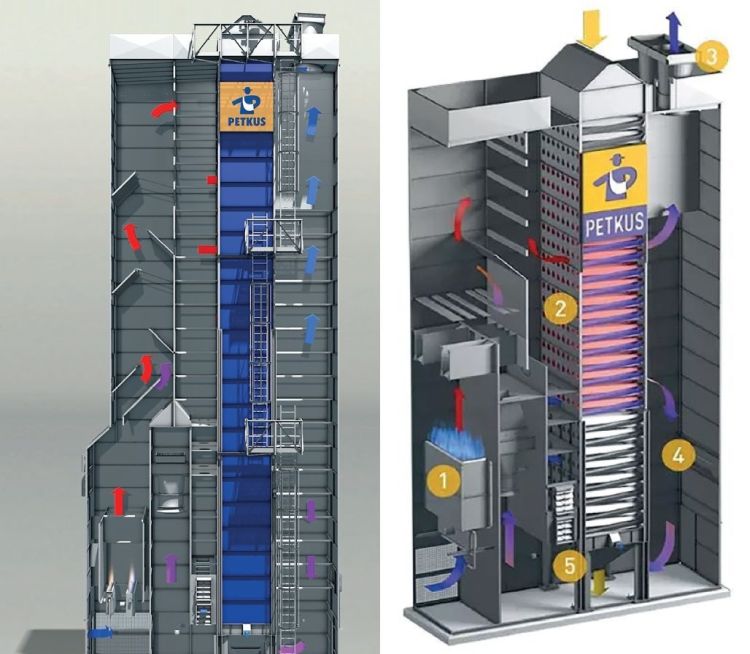
Légtechnikailag optimalizált szűkülő csatornákat (kaszkádokat) alkalmaznak, melyek az egyenletes hőellátáshoz állandó légsebességet szolgáltatnak a meleg levegő átáramlásához a terményoszlopban, egyúttal a kaszkádelemek mechanikusan olyan terményáramlást biztosítanak, mely által a termény keresztirányú keveredést kap az anyagvastagság érdembeli változása nélkül (3. kép, 2). A szárítógép utolsó harmadában a termény visszahűtése megoldott, és ezek a zónák a szárítógép optimális üzemeltetésének megfelelően változtathatók (3. kép, 5), valamint az ebből a visszahűtésből származó „hulladékhő” visszavezetésre kerül a hőellátó oldalra (3. kép, 4), ami által a gázfogyasztás csökkenthető, mivel rásegít a folyamatos üzemű fűtésre. A hőveszteségeket a szárítók külső lemezeinek szigetelésével csökkentik. Az előzőekben leírtak alapján egy modern szárítóberendezéssel akár30-40%-kal kedvezőbb gázfogyasztás érhető el. Az optimalizált légtechnikának és a kisebb töltőtömegnek köszönhetően sokkal kisebb villamosenergia-felhasználás érhető el a beépített ventilátorokra vonatkoztatva.
A régi rendszereknél alkalmazott „nyomott” meleg levegős ventilátorok helyett ma már a szárítók tetején elhelyezett „szívott” rendszerű ventilátorokat alkalmaznak (3. kép, 3). Összehasonlításként egy régi Bábolna szárítóba beépített villamos igény nagyságrendileg 60-70 kW, míg egy hasonló teljesítményű mai korszerű szárító 36–39 kW beépített villamos teljesítménnyel rendelkezik. Napjaink modern PLC-vezérelt szárítói pedig hozzáadják a maguk részét az emberi tényező kiküszöbölésére, hogy minél optimálisabb legyen a szárító üzemeltetése a belső-külső hatások figyelembevételével. Ma már a szárítók nagy része „automata” funkcióval tud működni, és „figyel” minden paramétert, így az üzemeltetés biztonsága is kiemelkedő, hiszen ha bármelyik paraméter rendellenes tartományba kerül, az automatika rögtön jelez, vagy leállítja a folyamatot a károsodások (mind a terményben, mind a berendezésben) elkerülése érdekében. Úgy vélem, hogy napjainkban nem kell kiemelni ezeknek az energetikai jellemzőknek a hatását az üzemeltetési költségekre, valamint a vezérlés optimális üzemeltetést adó feltételeire vonatkozóan, és akkor még nem beszéltünk a ma legfontosabbnak tartott fenntarthatósági hatásra és károsanyag-kibocsátásra. Itt tartunk napjainkban.
EZEKRE FIGYELJÜNKA MEGTERVEZÉSNÉL
Mit kell figyelembe vennünk egy szárítóberuházás megtervezésénél? Természetesen egyrészt a legfontosabb, hogy milyen terményt mekkora területen termelünk, és milyen ütemben takarítunk be. Korábban az adott terület terméshozamát és az aratási szezon napokra visszavetített idejét vettük alapul, de ez ma már megváltozott. Napjainkban a beruházók már nagyon nagy teljesítményű betakarítógépekkel rendelkeznek, melyek a termény tisztaságára is nagy hatással vannak modern cséplőrendszerükkel. Ebből kifolyólag tehát inkább az aratás napi teljesítménye a mérvadó, és ez határozza meg a szárítógép feldolgozási teljesítményét. Ez azért is fontos, hogy ne a szárítókapacitás (vagy tisztítókapacitás, ha nem kell szárítani) legyen a szűk keresztmetszet a technológiai sorban, mert az elhúzódó betakarítás veszélyezteti az aratás utáni talajművelési és vetési munkák optimális időbeni elvégzését. Ez szemléletváltást hozott a terményfeldolgozó technológiák és a szárítók kapacitásának méretezésében is. Alkalmanként egy-egy technológiasor túlméretezettnek is tűnhet az adott területhez, de a betakarítási időtényező, melyet a beruházók modern, akár precíziós gépekkel leredukáltak, mégis indokolják a nagyobb szárítási kapacitás megvalósítását.
AKTUÁLIS TRENDEK
A feldolgozási teljesítmény tisztázása után, ami most már talán nem is legfontosabb kérdés, nézzük meg az aktuális trendeket és kérdéseket, amelyek felmerülnek egy szárítóberuházásnál. Mindenki keresi a gáz- és villamosenergia-felhasználás minimalizálásának lehetőségeit, sőt, akár a gázfűtés nélküli lehetőségeket is. Ez nagy kihívás, főleg kukorica szárításánál (hazánkban ez a meghatározó), ahol folyamatosan nagyobb és állandó hőmennyiségeket kell bevinni a szárítási folyamatba, mivel nemcsak felületi nedvességet kell elvonnunk a terményből, hanem a belső, ún. kapillárisokból is ki kell csalogatnunk a vizet. A nedvesség elvonása kukoricánál jelen gyakorlat szerint átlagosan6-8 víz%, de akár 10 víz% is lehet, fajtától és szezontól függően. Az egyéb általános termények esetén (repce, búza vagy napraforgó) már nem jellemző – csak elvétve –, hogy szárítást érdemben kellene alkalmazni. (Bár hozzá kell tennünk, hogy a klímaváltozás hozza magával a maga hatásait, és megtörténik, hogy évjárattól függően csak pár víz% elvonást kell elvégezni a kukorica szárítása során is.)
A HŐMENNYISÉG KULCSKÉRDÉS
A nagyobb hőmennyiség biztosításhoz kell a nagyobb fűtési energia, melyet folyamatosan állandó hőmérsékletet tartva kell biztosítani a szárítóberendezésnek. Ellenkező esetben a szárítás nem lesz egyenletes, és vagy felülszárítunk (hosszú távú tárolás veszélyeztetése, melegedés-bogarasodás, bepenészesedés-károsodás stb.), vagy alászárítunk/túlszárítunk (indokolatlan többletenergia felhasználása, súlyvesztés a terményben, törtszemarány megnövekedésének esélye, beltartalom károsodása stb.), és kár érhet bennünket. Jelenleg a gázfűtés és annak vezérlése adja a legjobb feltételeket az egyenletes és állandó hőmérséklet biztosításához a szárítógépeknél. Természetesen ennek a nagyobb hőenergiának a biztosítására valósultak már meg egyedi és előremutató beruházások, melyek vezérlésüket tekintve is ki tudnak szolgálni szárítóberendezéseket, de a bekerülés költsége és a szárító környezetének helyigénye nagy kompromisszumot követel, így elterjedésüknek ez jelentős korlátot szab. Megvalósult faapríték-tüzelésű kazánrendszerek már léteznek (4. kép), melyek képesek rásegítést nyújtani a gázenergia felhasználásának csökkentésére, vagy akár kedvezőbb környezeti körülmények között ki is váltják, de ezek bekerülése nagyságrendileg még egyszer a szárítóberendezés költsége, illetve a megfelelő kondíciójú faapríték folyamatos biztosítása is gondot jelenthet.
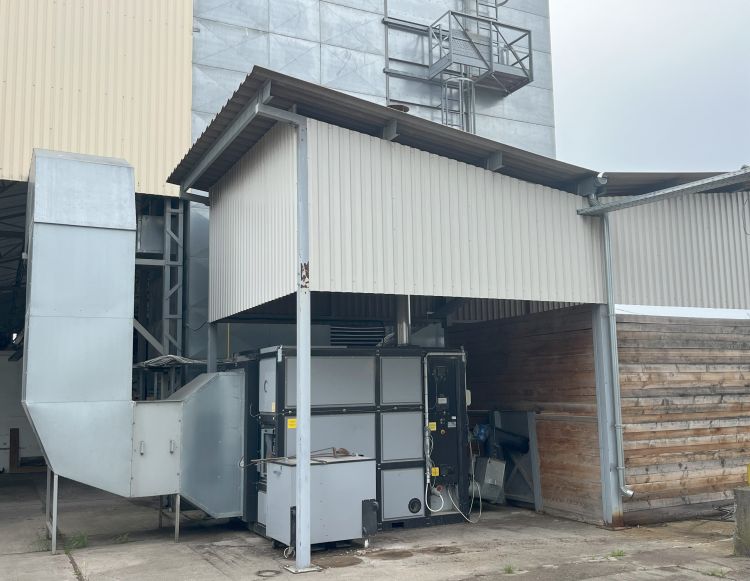
Ezeknél a rendszereknél tény viszont, hogy a gázfelhasználást nagyban tudják csökkenteni, és egy megtérülésszámítás alapja lehet a beruházás megvalósításának. Többször felmerül a szalmabálatüzelésű kazán beépítésére vonatkozó kérdés is, de ebben az esetben a kénképződés miatt elkerülhetetlen a kazán után utóégető beépítése, mert ha a kén a szárítás során elvont víz oxigénjével találkozik, akkor kénsav keletkezik, és nagyon rövid időn belül tönkreteszi a szárító horganyzott lemezeit. Tehát ez sem igazán versenyképes és jó megoldás szárító esetén, annál is inkább, mivel a szalmabála égése sem egyenletes, így nem ad állandó fűtő hőmennyiséget, ami miatt a vezérlés megoldása sem egyszerű a folyamatos és állandó hőbevitelhez. Elérhető megoldás lehet még a meleg vizes vagy termálvizes hőcserélős megoldás alkalmazása hazánkban (5. kép), de csak ott, ahol van!
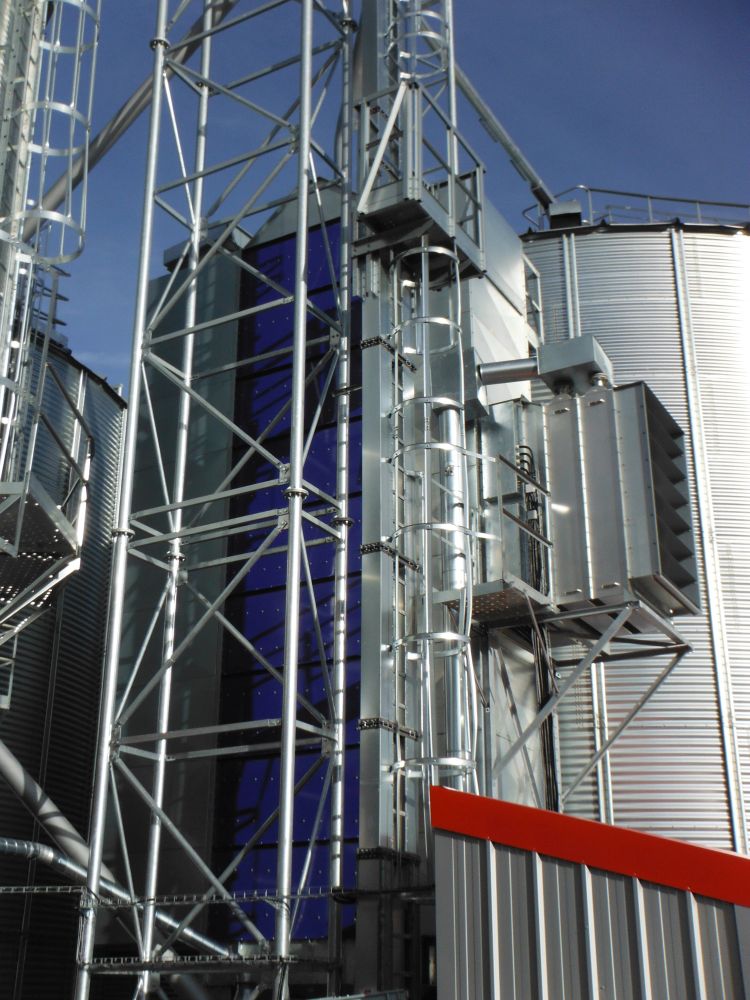
Ennek a hőellátó rendszernek a kialakítása külön tervezést és feltételeket indukál, mivel a termálvíz szárítógéphez történő juttatása megfelelő fűtőértékkel, és utána a víz visszajuttatása a hőcsere után ugyancsak nem egyszerű műszaki megoldást és ezzel együtt nem kis költséget képvisel. Meleg vizes hőcserélős rendszer valósult már meg biogázüzem mellett is, ahol a gázmotor hűtővize lett a szárító hőcserélőjében felhasználva. A hűtőrendszer kialakításának feltételei hasonlóak, mint a termálvíznél leírtak esetén, mindamellett ezek a rendszerek is csak fűtésrásegítésként szolgálhatnak a fűtőenergia-ellátásban.
A GÁZFŰTÉS MARAD, DE…
Egyelőre úgy néz ki, hogy a gázfűtés meg fog maradni a jövőt tekintve a kukorica szárítása miatt, de… Az előbb leírt megoldások alkalmazhatók alacsony hőfokú szárítások esetén! Tehát a fentiekben leírt és már egyedileg megvalósult faapríték-tüzelés vagy a termálvizes fűtés tökéletesen megfelel, ha maximum 60-70 fokkal kell fűtenünk, mint például napraforgó, repce (főleg faapríték esetén például, ha a tisztítás során keletkezett olajos ocsút bekeverjük) vagy esetenként búza, árpa szárításánál. Ebben az esetben a gyakorlat szerint a gázégőt ténylegesen nem is kell elindítanunk. Illetve kukorica feldolgozásánál is előfordulhat, ha olyan év van, amikor csak pár vízszázalékot kell elvonnunk, és a külső környezeti hőmérséklet is nyárias jellegű, és a gázégő szinte nem is üzemel. (Bár ilyen esetekben talán fájdalmasabb lesz a terméseredményről beszélni.)
VILLANY NÉLKÜL NEM MEGY
A villamosenergia-felhasználás alternatív megoldással történő csökkentése vagy kiváltása kapcsán a szárítók esetében egyelőre még nem beszélhetünk működő megoldásokról, annál is inkább, mivel folyamatos üzem esetén a szárítók éjszaka is üzemelnek. Tehát ha valaki napelemes megoldáson törné a fejét, annak gondolnia kell arra is, hogy például egy mai 15 t/ó teljesítményű szárítóba beépített 40 kW/h villamos teljesítményhez folyamatosan nemcsak nappal kellene biztosítania az energiát, hanem éjszaka is… Most jobban nem is fejteném ki, hogy ez milyen beruházási feltételek biztosításával járna, de véleményem szerint nyilvánvaló, hogy mai tudásunk és műszaki megoldásaink alapján egyelőre még sokáig nem ez lesz a fő fejlesztési irány.
KÖRNYEZETTERHELÉS
A szárítógép energiaellátásának és energetikai jellemzőinek tisztázása után a következő fontos kérdés a környezetterhelési mutatók tisztázása és az ebben a kérdéskörben felmerülő fejlődési kényszerek. Érdemben két tényező van, amit itt vizsgálnunk kell, ez a zaj- és a porterhelési mutatóknak való megfelelés. Ebben a kérdéskörben a szárítógép önmagában nem értelmezhető, mivel az mindig a szárítót kiszolgáló technológiai sorral együtt (termény- és anyagmozgató berendezések és tisztítógépek, valamint az azokat összekötő terménycsövezés-rendszerek) kerül megvalósításra, így tehát ezeket a paramétereket mindig együtt kell vizsgálnunk az egész technológiai sorral. Mivel azonban a szárítógép is része a technológiai sornak, és jelen témánk a szárítógép, így vegyük fókusz alá mint önálló egységet. Itt szeretném újból megjegyezni, hogy sokféle szárítógép van a hazai piacon, és sokféle megoldás van a szárítók működési rendszerének kialakítására. A következő részben a legjellemzőbb kaszkádrendszerű kialakítást vettem alapul, és annak működését igyekszem bemutatni.
ZAJTERHELÉS
A zaj tekintetében van a „legkönnyebb” dolgunk, mivel a mai modern szárítók, mint ahogy erre az előzőekben is hivatkoztam, szigeteltek, a hőenergia minél kedvezőbb felhasználása érdekében, így ez a szigetelés a zajkibocsátás tekintetében is jótékony hatású. A szárító esetében elmondható, hogy a szárítótest önmagában nem generál zajt. Amivel érdemben foglalkoznunk kell, az a gázégő és az elszívóventilátorok zajhatása. A gázégő esetében az a szerencse, hogy az a szárítógép alján kerül beépítésre, és a környező épületek és tereptárgyak árnyékoló hatásának, valamint a telepi teherforgalomnak köszönhetően nem jelent különösebb gondot mint zajforrás, bár számolnunk kell vele mint befolyásoló tényezővel. A ventilátorok tekintetében már más a helyzet. A kifúvóventilátorok általában a szárítógép tetején helyezkednek el, és ezeknek az égő működéséből és a légszállításból adódóan van zajkibocsátó hatásuk. Ezeket a ventilátorokat zajcsillapító dobokkal lehet ellátni, a kifúvás irányát kürtővel el lehet elfordítani, mely egyben a zaj irányát is elfordíthatja a védendő objektumok felől, valamint zajárnyékoló panelekkel lehet a kedvezőtlen zajhatást nagyon jó hatásfokkal kiküszöbölni (6. kép).
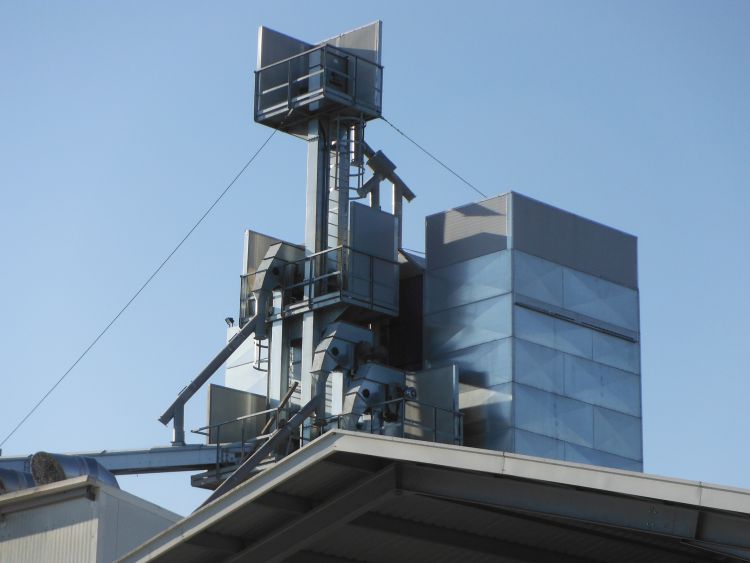
Ezen a területen jelentős innováció a jövőben nem várható, mivel a meglévő megoldások, ha szükséges, jól és költséghatékonyan alkalmasak a zajprobléma megoldására.
PORKIBOCSÁTÁS, LEVEGŐSZENNYEZÉS
A porkibocsátás tekintetében viszont már sokkal nagyobb jövőbeni kihívások és fejlesztések kerülnek előtérbe. A ma modernnek mondott szárítók mindegyike kielégíti a hatóságok által előírt határértéket, és ez alapján minden gond nélkül üzemelhetnek, de egyre inkább előtérbe kerül az a beruházói igény, hogy a szárítógép ennek ellenére közel nulla porkibocsátási értékkel működjön. A beruházó gyakran nem tartja elfogadhatónak az irodaépületen vagy a parkoló személyautók tetején a por vagy léha jelenlétét. Ez azért érdekes kérdés, mert, ahogy említettem, a szárító egy technológiai sor eleme, és nem lehet önmagában vizsgálni, de nem kikerülve ismét a kérdést: elemezzük a szárítógépet mint önálló egységet. A termény száradási folyamata során a magokon feltapadt sár és nedves léha, amit a tisztítógép fizikailag nem tud leválasztani, a szárítóban válik le a magokról, és mint könnyű anyag a ventilátor szívóhatására a kilépő levegővel távozik vagy távozna el a szárítóból. Ennek a könnyű anyagnak a levegőben való határérték alá csökkentésére különféle megoldások vannak, melyek gyártónként változnak. A végső mennyiséget természetesen még a betakarítás minősége és a tisztítógép beállítása is befolyásolja, de a porkibocsátás megfelelő gépbeállításokkal bőven hatósági határértéken belül tartható, a szárítógép nagy kilépő légáramához képest a porkoncentráció kezelhető. Ettől függetlenül viszont a légáramban mindig van valamekkora por- és léhamennyiség, amit a szárító ventilátorai 1520 méter magasból fújnak ki. Ez a valós koncentrációjánál látványosabb és kedvezőtlenebb hatású a környezetre, hiszen pár nap alatt ez az elenyésző pormennyiség már láthatóvá válik bármilyen felületen összegyűlve a szárító környezetében. Ez a jelenség indukálja azt a beruházói igényt, hogy nem foglalkoznak a környezetvédelmi megfelelőség igazolásával, hanem olyan rendszert kérnek, amelyik szinte zéró toleranciával rendelkezik porkibocsátási oldalon a szárítógépeknél. A jövőbeni trendek és fejlesztések ebbe az irányba fognak elmozdulni, és ezt az igényt lesz kénytelen minden gyártó kielégíteni. Ez kihívás lesz, hiszen nemcsak száraz por vagy léha hagyja el a szárítót, hanem a vízelvonás révén egy nedves por-léha elegy, így a leválasztórendszernek egyben a szárító kifúvóventilátoraival kombináltan öntisztítónak is kell lennie (7. kép), mivel a szárító üzemeltetésének több napon vagy héten keresztül folyamatosnak kell lennie.
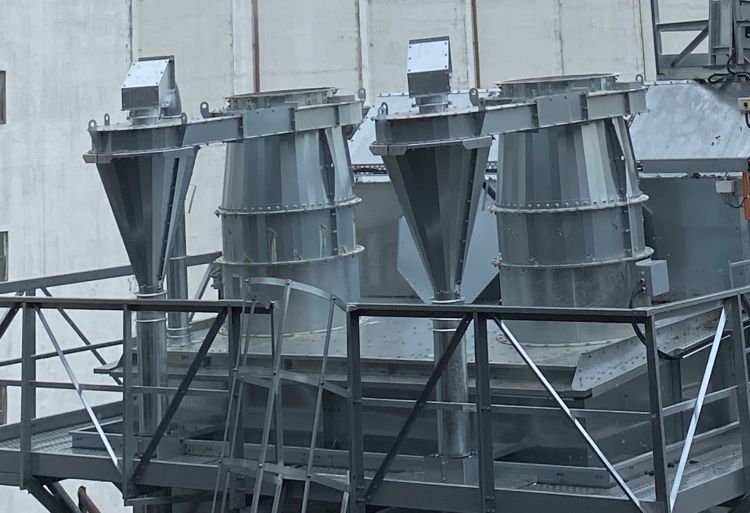
JÖVŐBENI FEJLESZTÉSEK
A jövőbeni fejlesztéseket még egy tényező határozhatja meg: milyen más új termények jelennek meg hazánkban, amikhez a szárítógépet vagy szárítási folyamatot hozzá kell igazítani. Mire gondoljunk itt? Például pár éve nagyobb mennyiségben megjelent a cirok, melyet ugyancsak szárítani kell. Ez sok kihívást jelentett, mivel a szárítókezelőkkel együtt kellett megtanulni, miként és milyen feltételekkel lehet üzembiztosan szárítani a cirokmagot. Változik a klíma, változik a régóta stabilan termelt termények jövedelmezősége, és a gazdák is keresik a kiutat más, jobb jövedelmezőséget adó növények termesztésével, melyek érinthetik a szárítóberendezések megfelelőségét is ezekre az újabb kihívásokra. A jövőt tekintve tehát az alternatív energiaellátás tekintetében vannak részeredmények, de inkább az üzemeltetés optimalizálásával vagy a szárítási folyamat vezérlésének a fejlesztésével nagyobb sikert lehet elérni az üzemeltetési energiák csökkentésére vonatkozóan. A környezetvédelmi megfelelőségnek pedig csak a beruházói igény és annak kompromisszumos elfogadása szabhat határt, amennyiben a hatósági előírások nem állítják irreális határértékeknek való megfelelés elé a gyártókat. Egy biztos: a fejlesztési irányok keresése és a szárítási folyamat optimalizálása ebben a szektorban is állandó feladat, de csak olyan megoldást lehet innováció alá vonni, és sorozatgyártásba tenni, amit a beruházók megfizetnek, és amiben a megtérülést is látják.
Gergely Sándor