Az additív gyártás, közismert nevén a 3D nyomtatás kulcsfontosságú fogalommá vált az off-highway iparágban. Az összes jelentős építőipari, erdészeti és mezőgazdasági gépgyártó, valamint OEM-partnereik használják ezt a megközelítést a prototípus- és kisszériás gyártáshoz, sőt egyesek már teljesen beépítették a 3D nyomtatást a tömeggyártásba is.
November 12. és 18. között a németországi Hannoverben megrendezésre kerülő SYSTEMS & COMPONENTS lesz a vezető helyszín az ipari 3D nyomtatás iránt érdeklődők, mobil gépek beszállítói és felhasználói számára.
Egyedi elérhetőség, alkalmazkodóképesség, kis gyártási mennyiségek, valamint nagyfokú alaki és formai szabadság – az additív gyártás drasztikusan lerövidítheti a fejlesztési időt, és költséghatékonyan gyárthat rendkívül összetett alkatrész-geometriákat. A legújabb fejlesztések egyre nagyobb érdeklődést váltanak ki az off-highway iparágakból, a 3D nyomtatás egyrészt betölti a gyors prototípusgyártási rést, és arra készül, hogy jelentősen megváltoztassa az ipari értékláncot az egész iparágban. A hagyományos szubtraktív gyártással ellentétben, ahol a fölösleges anyagot marással, esztergálással vagy csiszolással távolítják el, az additív gyártás rétegenként építi be az alapanyagot az alkatrész kialakításához. Különböző eljárásokat alkalmaznak, és a felhasznált anyagok spektruma a műanyagtól a fémeken át a kerámiáig terjed.
ÚJFAJTA TERVEZÉSI SZABADSÁGA FEJLESZTÉS SORÁN
A hannoveri rendezvényközpont kiállítói a már ismert por- és huzalalapú technológiák mellett innovatív anyagkombinációkon is dolgoznak, hogy a 3D nyomtatás határait feszegessék. Egyikük például a „binder jetting” technológiát, egy additív eljárást alkalmaz a homok öntőformák gyors előállítására, amelyet például tengelyházak vagy kerékagyak kiváló minőségű öntésére használnak. A 3D öntőformák homokkal történő előállítása döntő előnyökkel jár, ezenkívül az öntvények kialakítása a szokásosnál összetettebb lehet.
A homoköntvények folyamatos gyártására alkalmas nyomtatóberendezéseket már beépítették az off-highway területén dolgozó öntödék és prototípus-műhelyek, valamint az OEM-gyártók gyártósoraiba.
A SYSTEMS & COMPONENTS és a párhuzamos Agritechnica szakkiállításon a mezőgazdasági gépgyártók és OEM-partnereik, akik már most is közvetlenül nyomtatnak alkatrészeket, teljes mértékben kiaknázhatják az additív gyártásban rejlő lehetőségeket. Az olyan technológiák, mint a „Fused Deposition Modeling” (FDM) vagy a „Selective Laser Sintering” (SLS) lehetővé teszik a gyártási minőséghez közeli anyagok felhasználását a prototípusok és a sorozatgyártás előtti alkatrészek gyártásához, amelyek aztán az ipari nagyüzemi gyártást képviselik.
Az additív gyártás olyan különleges tulajdonságokat kínálhat, amelyek a hagyományos gyártás során nem találhatók meg, mint például a hőre lágyuló poliuretánból (TPU) készült rugalmas csillapítóelemek, a nagy szilárdságú szálerősítésű műanyagból készült motorkerékpár-borítások vagy a vezetőfülke felszerelésében több szabadságfokot lehetővé tevő szerelvények. A 3D nyomtatás olyan alkatrészek előállítására is használható, amelyek hagyományos fröccsöntéssel nem állíthatók elő egy darabból.
ADDITÍV GYÁRTÁS IPARI ALKALMAZÁSBAN
Az ipari additív gyártás egyik példáját jelentik a járműspecifikus vezérlőkonzolok, mint például az IBL Hydronic által gyártottak, amely cég mindössze egy hónap alatt fejezte be egy vezérlőmodul kifejlesztését, és mutatta be azt a mezőgazdasági gépészeti ágazatban működő megrendelőnek. A házrészeket SLS segítségével nyomtatták ki, összeszerelték, és bőrből készült karfával látták el. Annak érdekében, hogy ne csak funkcionális, hanem vizuálisan is vonzó legyen, a felületet textúrázták, az alkatrészeket pedig festették és polírozták. Az eredmény: egy bőrszerű textúra, amely vizuálisan feldobja a felületet és a dizájnt. A kisebb egyedi alkatrészek, például a fehér és narancssárga billentyűk esetében sztereolitográfi át (SLA) alkalmaztak, egy olyan additív technológiát, amely lehetővé teszi az átlátszó alkatrészek nyomtatását. Így a megvilágított figyelmeztető lámpákat közvetlenül a billentyűzetbe lehetett integrálni.
A példa azt is mutatja, hogy az additív gyártás során a 3D nyomtatási anyagok széles skálájára van szükség. Míg sokféle alkatrésztípus kizárólag műanyagból is előállítható, a fémek az additív gyártási eljárások egyik legkeresettebb anyagai. Nem meglepő, hogy tulajdonságaik miatt ideális választást jelenthetnek az igényes alkalmazásokhoz, mivel teljesítményt és szilárdságot kínálnak. A fémek természetüknél fogva jobban ellenállnak a terepjáró alkalmazásokban fellépő feszültségeknek, hőmérsékleteknek és nyomásoknak, így a mobil gépek hajtáselemeihez szükséges szilárdságú alkatrészek gyárthatók. Az alumínium különösen alkalmas a hatékony könnyűszerkezetes építésre.
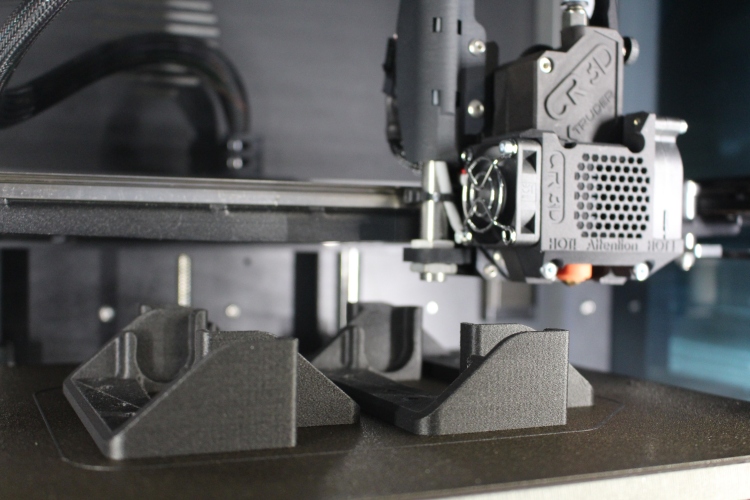
GÉPEK EGY ÚJ SÚLYOSZTÁLYBAN
A hőcserélőktől a hűtőbordákig a teljesen funkcionális prototípusok vagy a szerszám- és szerelvénygyártás esetében a 3D fémnyomtatás lehetővé teszi az összetett geometriájú, üregekkel, mélyedésekkel és részletes belső szerkezetekkel rendelkező alkatrészek létrehozását további szerszámok, egyéb bemeneti anyagok vagy további összeszerelési lépések nélkül, közvetlenül egy digitális tervezési fájlból, a CAD modellből, minimális súly és maximális merevség mellett. Az eljárás egy fókuszált lézersugárral olvasztja meg a fémport, és ahogy a fém megszilárdul, egy új porréteg kerül fel, ami egy homogén 3D alkatrész előállítását eredményezi.
A feltörekvő additív gyártási eljárások közé tartozik a „fémkötőanyagsugárzás” (MBJ). A John Deere a HPMetal Jet S100 technológiáját használja a traktorok üzemanyagrendszere szélsőséges időjárási körülmények között is működő szelepeinek gyártására. A „szelektív lézerolvasztáshoz” (SLM) hasonlóan az eljárás egy rétegenként felépített porágyat használ, de ahelyett, hogy a port lézerrel megolvasztaná, a nyomtatófej kötőanyagcseppeket juttat a meghatározott pozíciókba, amelyek a port rétegről rétegre megkötve alkotják az alkatrészt. Az így kapott „zöld alkatrészt” hagyják megszilárdulni, majd szinterezik, eltávolítva a kötőanyagot, és így jön létre a kész alkatrész. A HP 3D nyomtatói másodpercenként akár 630 millió nanorészecskényi kötőanyagot is képesek pontosan felhordani a porágyra. A John Deere prototípusok készítéséhez is használja a technológiát, hogy tesztelje és finomhangolja az olyan alkatrészeket, mint például a szélvédőtartók. „A mezőgazdasági iparban az elsők között vagyunk, akik a 3D nyomtatást mind a prototípusgyártás, mind az alkatrészek végső gyártása során kihasználják” – hangsúlyozza dr. Jochen Müller, a John Deere globális digitális mérnöki tevékenységének vezetője.
A HATÉKONY KARBANTARTÁS KULCSA
A SYSTEMS & COMPONENTS másik kulcsfontosságú témája az igény szerinti pótalkatrészek és azok gyártása a vevőszolgálat számára. Egyre több pótalkatrész gyártható 3D nyomtatóval, amely pontosan megfelel az ügyfél igényeinek, és megfelel az eredeti minőségének. Ennek előnye, hogy a pótalkatrészeket csak adatmodellként kell létrehozni és tárolni, a gyártás pedig szükség szerint történhet. Különösen a régebbi mezőgazdasági gépek esetében, ahol az elhasználódott alkatrészek hagyományos gyártási módszerekkel már nem gyárthatók hatékonyan, előnyös a 3D nyomtatás.
Az additív gyártásban rejlő teljes potenciál csak a berendezések, anyagok és eljárások összehangolt fejlesztésével valósítható meg. A jelenleg használt anyagok gyakran nem felelnek meg a mobil gépek sokrétű követelményeinek, ahol például a rugalmasságot, a hőmérséklet-stabilitást és a mágneses tulajdonságokat kell egy alkatrészben kombinálni. Ezenkívül a legtöbb acél és ötvözet még nem nyomtatható ki sikeresen, mivel repedések keletkezhetnek, ami két vagy több anyag additív összekapcsolásakor még hangsúlyosabb probléma.
„A 3D nyomtatással történő többanyagú gyártás még gyerekcipőben jár. A technológia áttörésének legnagyobb akadálya, hogy nem lehet az anyagokat a kívánt módon kombinálni” – hangsúlyozza prof. dr. Thomas Tröster, a Paderborni Egyetem Könnyűszerkezetes építés hibrid rendszerekkel (ILH, Institut für Leichtbau mit Hybridsystemen) és az Additív Gyártási Intézet (PIAF, Paderborner Institut für Additive Fertigung) elnöke.
A Paderborni Egyetem által vezetett kutatócsoport ennek a forradalmi technológiának az ipari alkalmazásait fejleszti. A Tröster professzor által koordinált MADE-3D (Multi-Material Design using 3D Printing) projekt célja, hogy az additív gyártást a következő szintre emelje, több, különböző fizikai tulajdonságokkal rendelkező anyag felhasználásával. A cél az, hogy a rendkívül összetett, könnyűszerkezetes alkatrészek tervezésének soha nem látott szabadságát tegye lehetővé, ami a jövőben egyértelműen előnyös lehet az off-highway ágazat számára is.
A DLG cikke alapján összeállította Fodor Mihály